Predictive Maintenance: 8 Beispiele aus der Praxis
Was bedeutet der Begriff und in welchen Bereichen wird diese Methode eingesetzt?
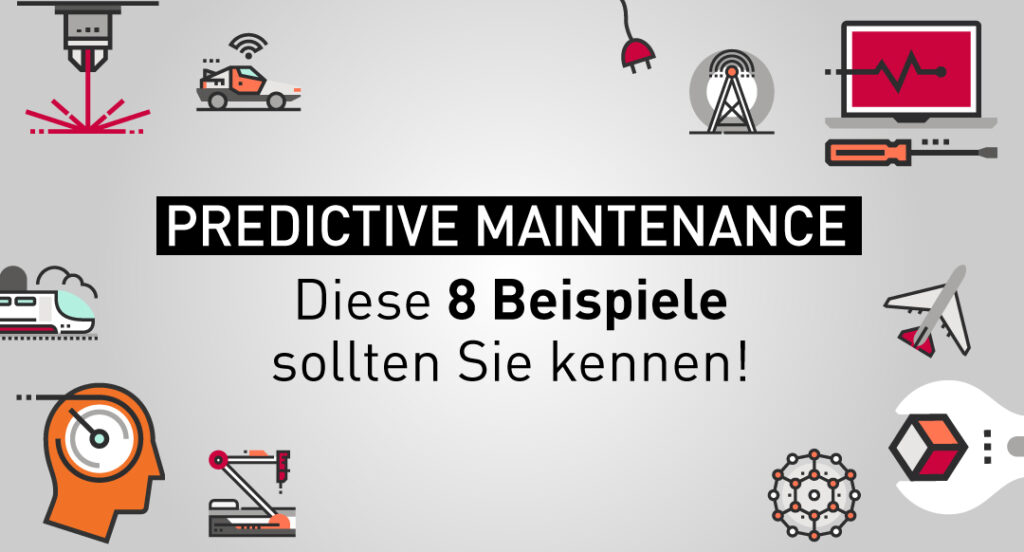
Herkömmliche Wartungen sind sehr zeitaufwändig und kostenintensiv. Denn sie werden nach festgelegten Intervallen durchgeführt oder erst dann in die Wege geleitet, wenn es bereits zu einem Maschinenausfall gekommen ist.
Da Maschinen innerhalb dieses Zeitraums nicht produktionsbereit sind, entstehen hohe wirtschaftliche Einbußen. Trotz dieser Nachteile setzen nach wie vor zahlreiche Unternehmen diese Wartungsmethoden ein.
Predictive Maintenance – die Lösung des Problems?
Die sog. Predictive Maintenance ist eine der Schlüsselinnovationen von Industrie 4.0. Was genau diese Methode von herkömmlichen Verfahren unterschiedet, erklären wir im nächsten Abschnitt.
Aber schon mal so viel: Predictive Maintenance wurde von 2020 noch von nur 40 Prozent der Unternehmen genutzt. Mittlerweile ist der wichtige Industrietrend eindeutig im deutschen Maschinenbau als Ausrüster-Branche angekommen – 81% der befragten Unternehmen befassen sich bereits intensiv mit diesem Thema. Dies zeigt die Studie des Verbands Deutscher Maschinen- und Anlagenbauer (VDMA) und der Unternehmensberatung Roland Berger und der Deutschen Messe.
Unser Ziel ist es, Ihnen in diesem Artikel einen Überblick über die wichtigsten Begriffe, Funktionen sowie Chancen und Risiken der Predictive Maintenance zu geben. Diese Informationen unterlegen wir mit praktischen Beispielen aus verschiedenen Branchen, in denen die Predictive Maintenance zahlreiche Chancen bietet.
Was ist Predictive Maintenance?
Die im Deutschen als vorausschauende Instandhaltung bezeichnete Methode sammelt Maschinen- und Prozessdaten und wertet diese in Echtzeit aus. Die Auswertung von Maschinendaten in Echtzeit nennt man Condition Monitoring. Dies geschieht mithilfe ausgefeilter Algorithmen und Sensorik. Die größte Errungenschaft dieser Technologie ist es, dass Prognosen exakter getroffen und Ausfallzeiten reduziert werden können.
Die Technologie misst insbesondere Daten zu Vibration, Druck, Temperatur u. ä. Aus diesen aktuellen Maschinendaten in Kombination mit Vergangenheitsdaten ergeben sich Muster in den Betriebsparametern. Diese machen wiederum eine Vorhersage der Lebensdauer oder eine Optimierung der Maschine möglich. Der Instandhalter kann somit bereits informiert werden, bevor es zu einem Problem der Maschine kommt. Predictive Maintenance vermeidet unvorhergesehene Ausfälle.
Wartungen werden genau zu dem Zeitpunkt durchgeführt, bei dem sie sich nur gering auf die Produktion auswirken. Ziel ist es, den Personal- und Materialaufwand so gering wie möglich zu halten.
Was sind die Chancen der Predictive Maintenance?
Mithilfe einer Predictive-Maintenance-Lösung kann ein Unternehmen eine höhere Wirtschaftlichkeit erzielen. Dafür sorgen die folgenden Faktoren:
- Reduzierung von Stillstandszeiten
- Erhöhung der Anlagenverfügbarkeit
- Reduzierung der Kosten für ungeplante Ausfälle
- Erhöhung der Lebensdauer der Maschinen durch regelmäßige Wartung
- Perfektionierter Wartungszeitpunkt: Dadurch, dass Maschinendaten ununterbrochen erfasst werden, kann der beste Zeitpunkt für eine Wartung bestimmt und in den Prozess eingebunden werden.
- Höhere Produktivität: Verbesserung der Maschinenleistung durch Analyse der Daten
Was sind die Risiken der Predictive Maintenance?
Das größte Risiko der Predictive Maintenance ist die damit verbundene Herausforderung: Unternehmen müssen riesige Datenmengen (Big Data) erheben, um eine zuverlässige Aussage über den Zustand von Anlagen und deren Störungen zu machen. Da gesammelte Daten über Temperatur, Feuchtigkeit, Vibrationen etc. verschiedene Formate haben, wird die Verarbeitung dieser Daten oft zur Herausforderung.
Was unterscheidet Predictive Maintenance von anderen Wartungsmethoden?
Im Gegensatz zur Predictive Maintenance, die bereits eingreift bevor es zu einem Ausfall kommt, folgt die sog. reaktive Wartung einem anderen Prinzip: Sie greift erst dann, wenn bereits Fehler bzw. Störungen an Maschinen und Anlagen aufgetreten sind. Nachdem es zu einem Fehler gekommen ist, folgen Problemanalysen und schließlich Strategien zur Beseitigung der Störung.
Vorteil dieser Methode ist insbesondere deren einfache Umsetzbarkeit. Die Nachteile sind jedoch nicht zu vernachlässigen: Reaktive Wartung kann Maschinenausfälle nicht verhindern, wodurch es zu längeren Stillstandszeiten kommt. Diese verlängern sich möglicherweise nochmals dadurch, dass Ersatzteile noch nachträglich bestellt werden müssen.
Das dritte Konzept, das neben der Predictive Maintenance und der reaktiven Wartung besteht, ist die präventive Wartung. Deren oberstes Ziel ist es, Stillstandszeiten zu vermeiden. Im Gegensatz zur Predictive Maintenance werden zur Bestimmung des perfekten Wartungszeitpunkts aber keine Echtzeitdaten genutzt, sondern Wartungen nach zuvor festgelegten, starren Intervallen durchgeführt.
Vorteil ist die Einfachheit der Planung. Nachteil dieses Ansatzes allerdings ist, dass das Unternehmen auch Teile, die noch längere Zeit ohne Probleme funktionieren würden, austauscht. Dies ist aus Kostensicht ineffizient.
Welche Praxisbeispiele mit Predictive Maintenance gibt es?
Windkraftanlagen
Predictive Maintenance kann Ausfälle von Windkraftanlagen heutzutage fast vollständig vermeiden. Denn ausgefeilte Algorithmen sind in der Lage, eindeutige Prognosen über Ausfallwahrscheinlichkeiten zu liefern. Dazu führen sie Schwingungsanalysen von verschleißgefährdeten Bauteilen durch.
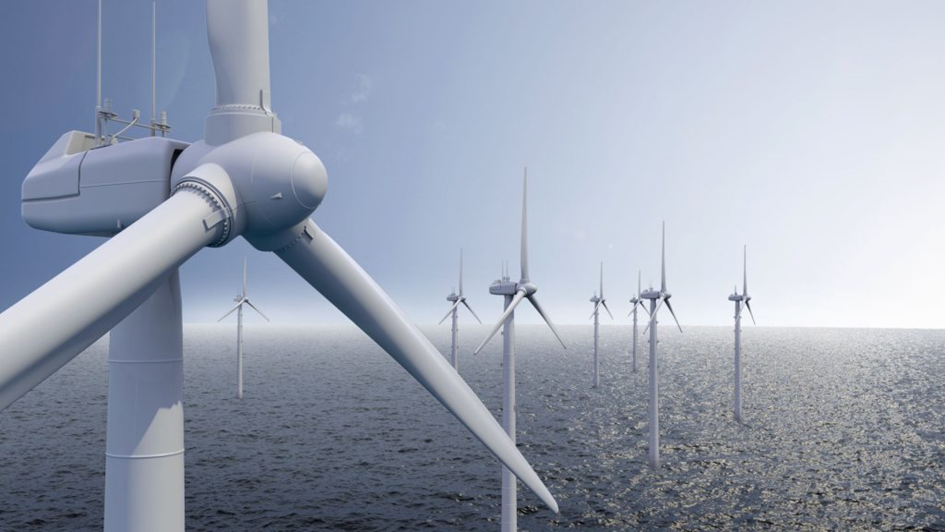
Kraftfahrzeuge & vernetztes Fahrzeug
Auch bei der Wartung von Kraftfahrzeugen gewinnt Predictive Maintenance an Bedeutung: Sensoren, die sich beispielsweise im Motor oder im Fahrwerk befinden, machen eine Datenanalyse möglich. So kann man ein defektes Teil bereits beim nächsten Besuch der Werkstatt austauschen, noch bevor es vollständig ausfällt. Es ist somit möglich, teuren Reparaturen vorzubeugen.
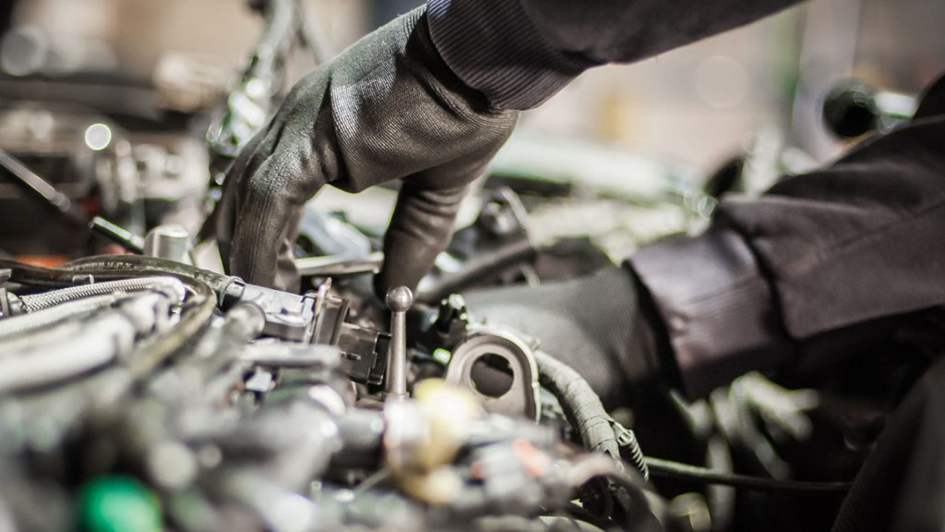
Dies lässt uns auch schon zum nächsten Punkt überleiten, dem vernetzten Fahrzeug: Heutzutage sind zahlreiche Sensoren in Autos verteilt. Diese große Menge an Daten (Big Data) wird auf direktem Weg – automatisch – an den Hersteller oder Autohändler weitergeleitet. Daten werden beispielsweise gesammelt, um einen Überblick über den Zustand des Autos zu bekommen oder Fahrzeugfehler frühzeitig zu entdecken.
Elektromobilität
Hierbei ist es möglich, eine Verschlechterung des Akkus zu erkennen und vorherzusagen, wann die Leistung der Batterie nachlässt (Zustandsbewertung). Die späteren Auswirkungen auf die Mobilität des Fahrzeugs können exakt festgestellt werden.
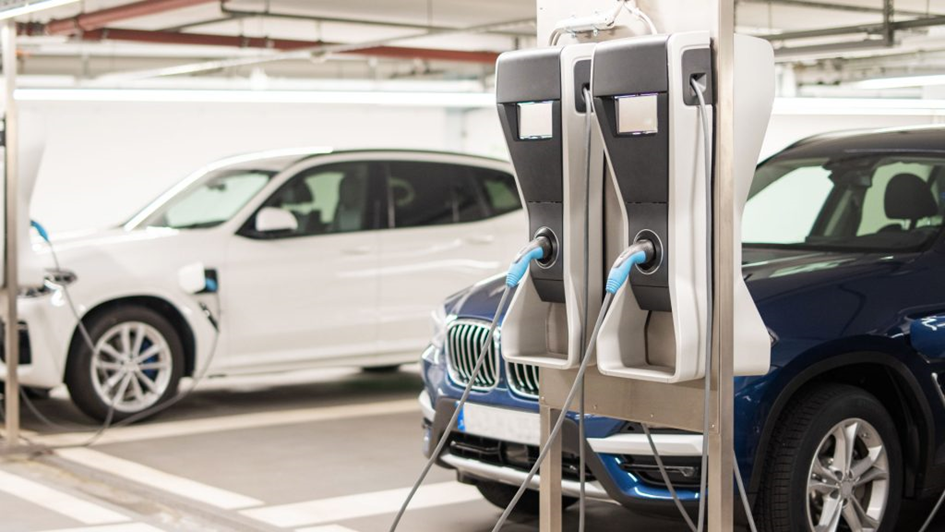
Luftfahrt
In der Luftfahrt können Turbinen oder Pumpen bereits vor einem endgültigen Defekt ausgetauscht werden. Insbesondere für Airlines ist es wichtig, Fehler frühzeitig zu erkennen. Denn es entsteht – aufgrund der hohen Fixkosten – ein großer wirtschaftlicher Schaden, wenn ein Flugzeug nicht betriebsbereit ist.
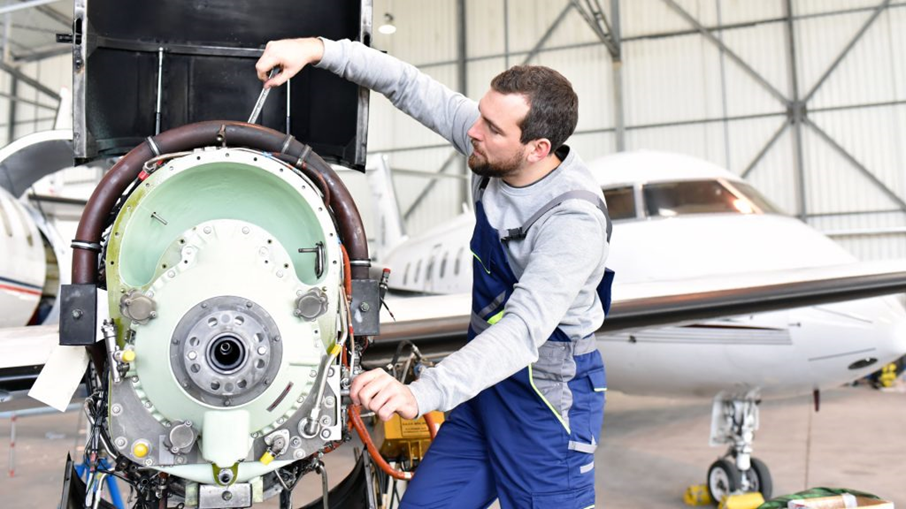
Schienenverkehr
Mithilfe der Predictive Maintenance ist es im Schienenverkehr möglich, ungeplante Ausfälle von Zügen zu vermeiden. Beispielsweise kann ein modernes, fahrbares Überwachungssystem Spurlücken erkennen oder den Zustand von Weichenmaschinen stetig überwachen. So kann man – bei Einsatz vorausschauender Planung – Verzögerungen im Betriebsablauf vermeiden, wenn man Symptome einer Verschlechterung frühzeitig erkennt. Auch Ersatzteile können bereits vor einem möglichen Ausfall bestellt werden.
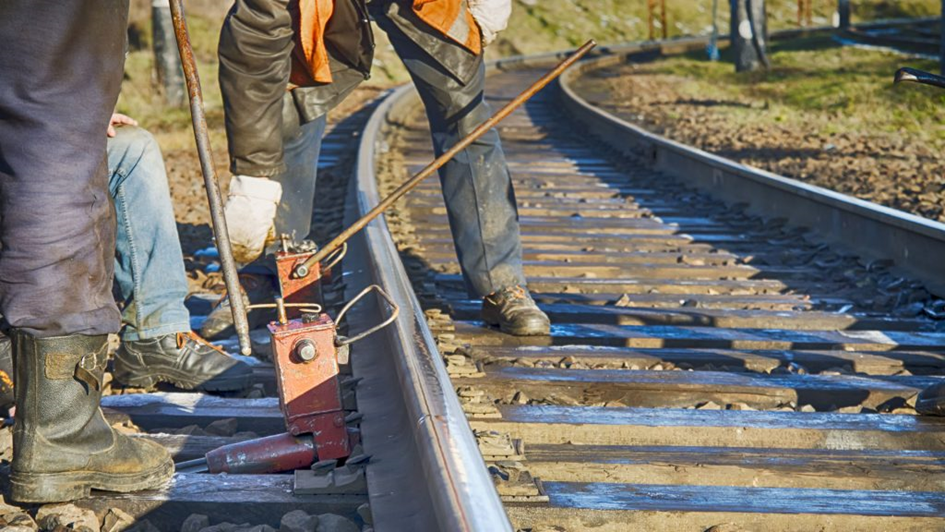
Versorgungsunternehmen
Mithilfe von Predictive Maintenance kann man in dieser Branche Frühwarnzeichen von der Versorgungs- oder der Nachfrageseite des Netzes aus erkennen. Die Unternehmen können diese dann beheben, bevor es zu Ausfällen kommt. Die Folge ist die Vermeidung kostenintensiver Reparaturen und die Reduzierung von Kundenbeschwerden.
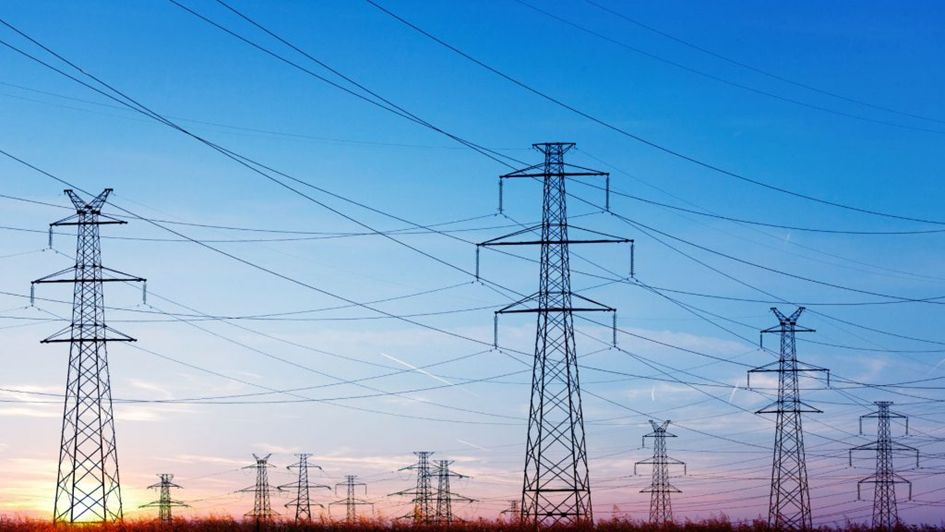
Produktion
Wie bereits weiter oben erwähnt, ist der Einsatz der Predictive Maintenance insbesondere im Produktionssektor nützlich. In Maschinen und Anlagen sind Sensoren verbaut, die Big Data sammeln. So können Algorithmen Fehler frühzeitig erkennen, diagnostizieren und vermeiden.
Eine geeignete Instandhaltungssoftware, z.B. imaso® maintenance von ccc software gmbh, kann dabei helfen, diese Datenerfassung zu optimieren. Die Lösung hilft dabei, die Daten aus verschiedenen Quellen zusammenzuführen und auszuwerten.
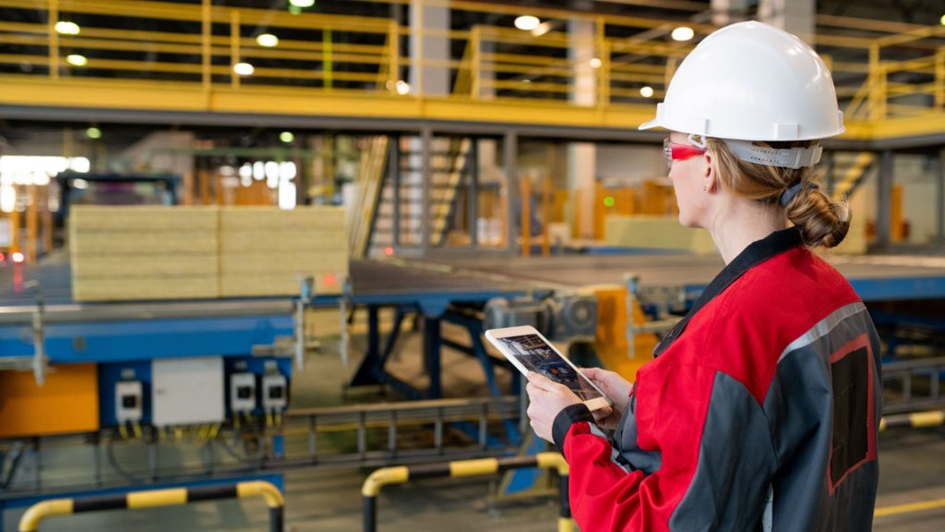
Öl- und Gasunternehmen
In der Öl- und Gasbranche werden beispielsweise Tiefwasserstandorte zum Problem: Da man dort oftmals keinen Einblick in den Zustand der Ausrüstung erhalten kann, bieten Big Data und Predictive Maintenance eine Lösung. Denn diese sorgen für einen besseren Überblick über die Ausrüstung, sodass man Ausfälle der Geräte vorhersagen kann. Dadurch kann auch die Lebensdauer der Systeme erhöht werden.
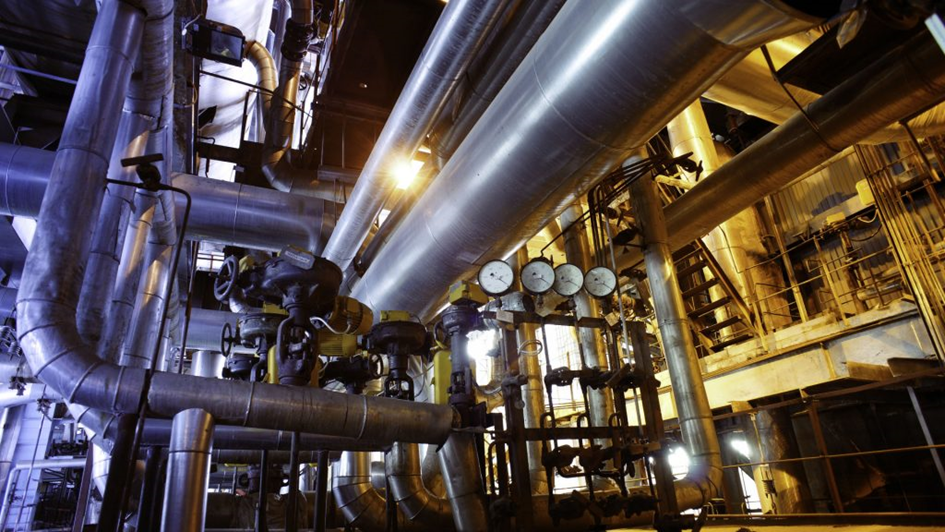
Fazit: Predictive Maintenance
Das volle Potential der vorausschauenden Instandhaltung ist noch nicht ausgeschöpft. Wie an den Beispielen deutlich wurde, kann sie zu einem sinnvollen Unterstützer in verschiedenen Branchen werden. Stück für Stück kommen in immer mehr Bereichen Technologien zur Datenerfassung und -auswertung zum Einsatz. Insbesondere durch KI können damit immer besser Prognosen erstellt werden, die teure Ausfälle verhindern sollen.
Einen kleinen Ausblick darf man bereits jetzt wagen: Die Bedeutung und Wichtigkeit der Predictive Maintenance wird für Unternehmen auch in Zukunft noch weiter steigen.
Autorin:
Sorina Serban, ccc software gmbh